One Solution for All Your Needs

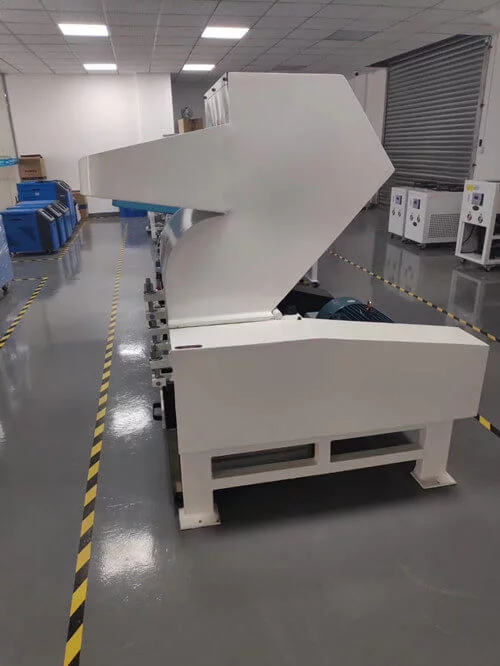
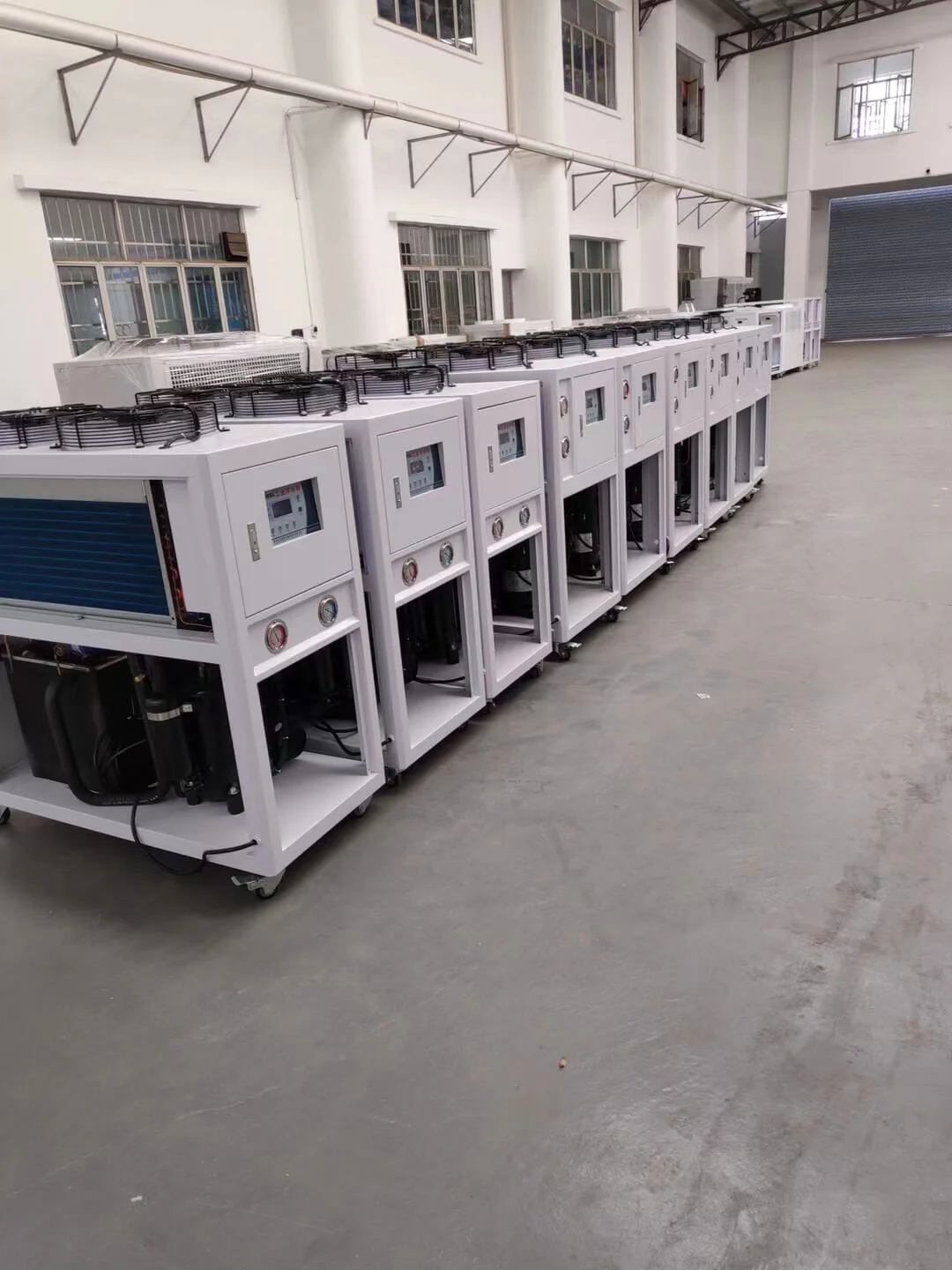
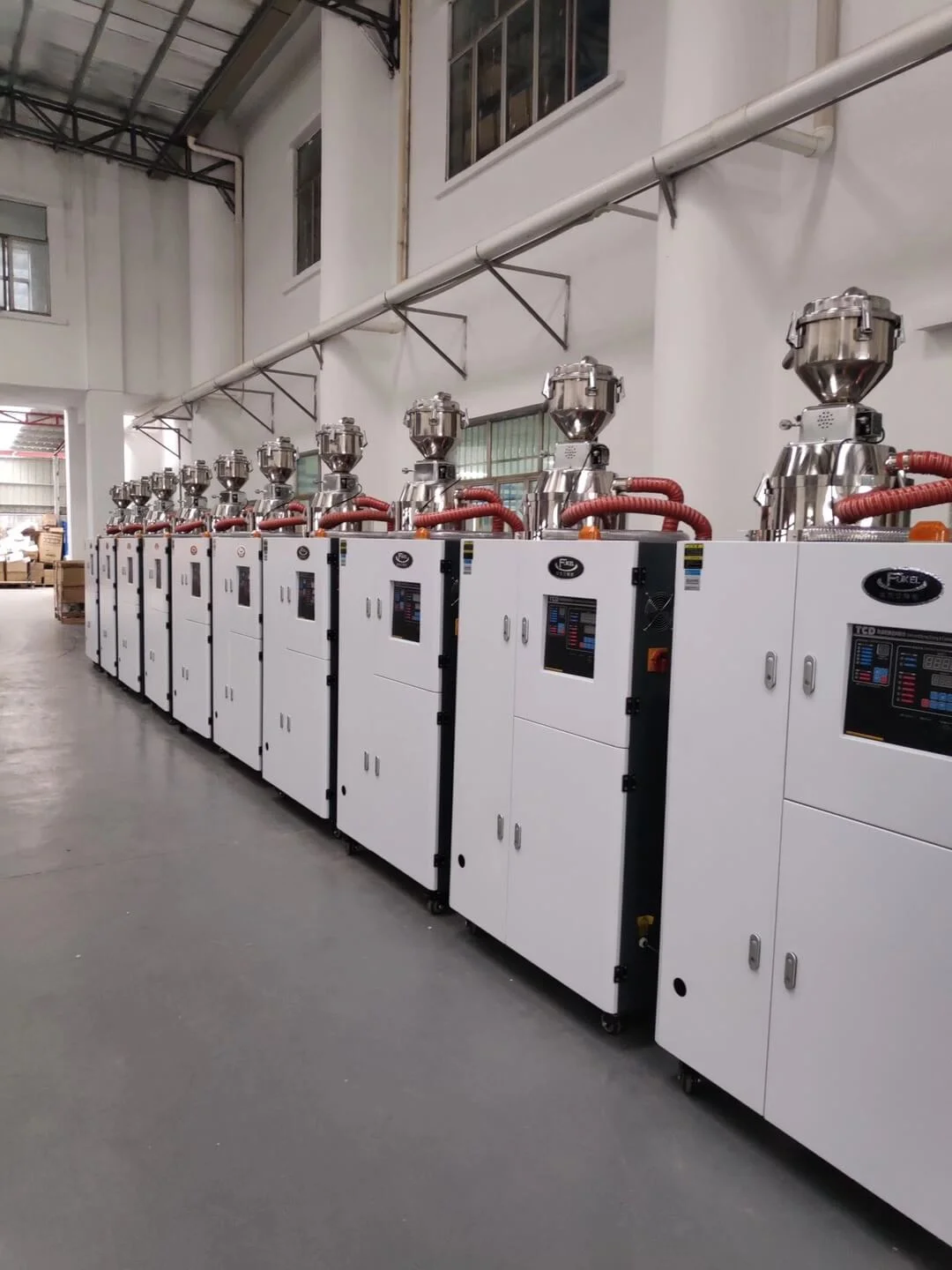
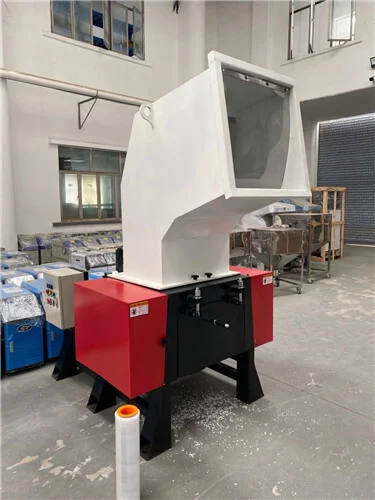
Factory ShowRoom
Trusted Manufacturer of Plastic Auxiliary Equipments From China.
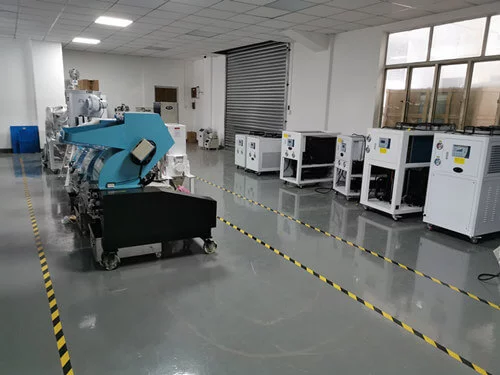
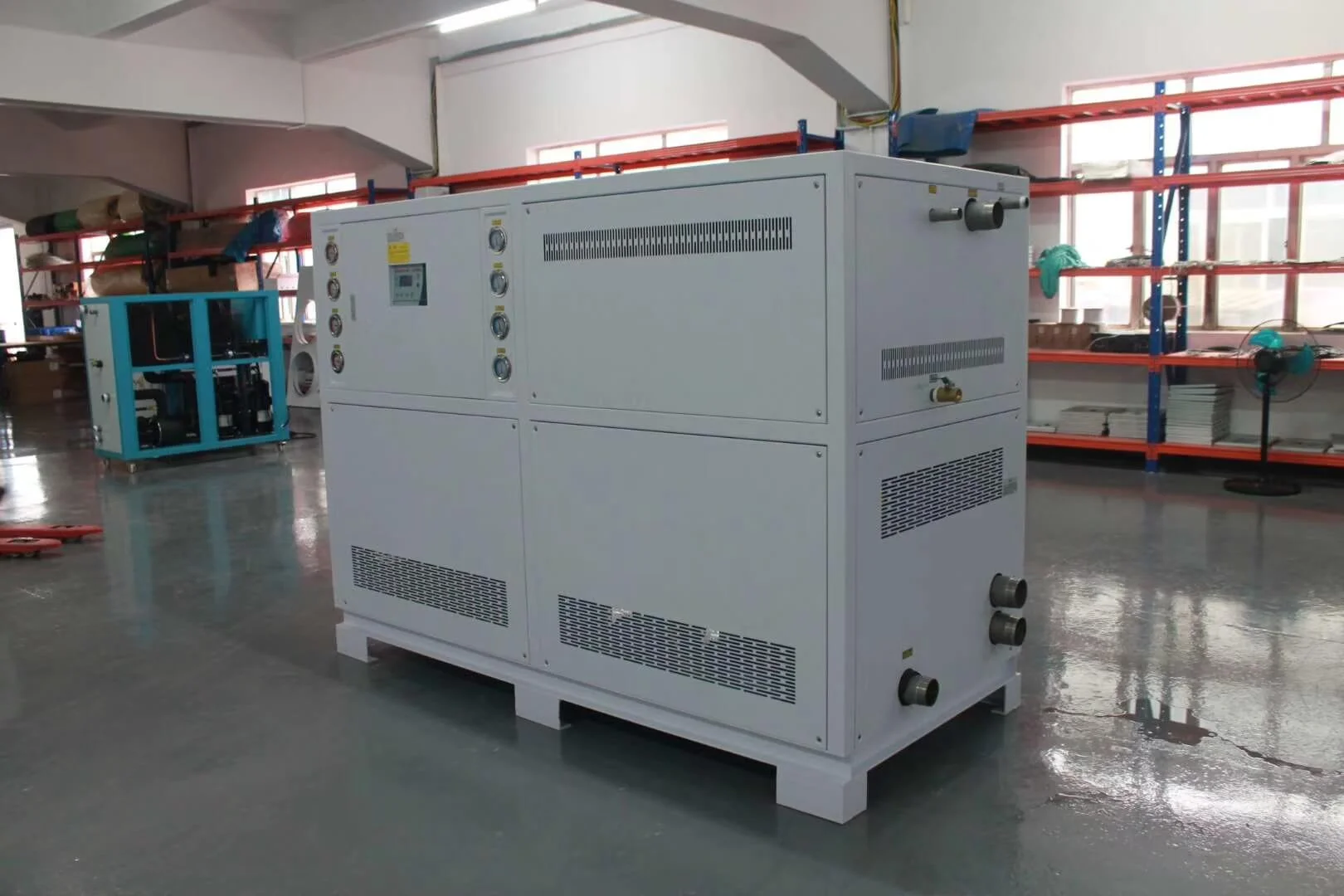
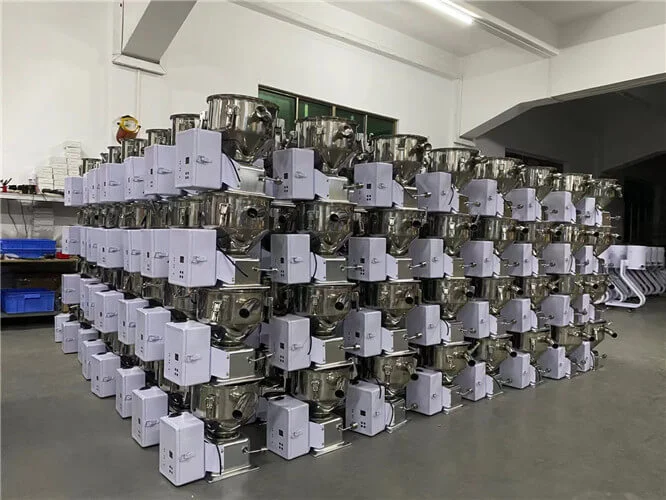
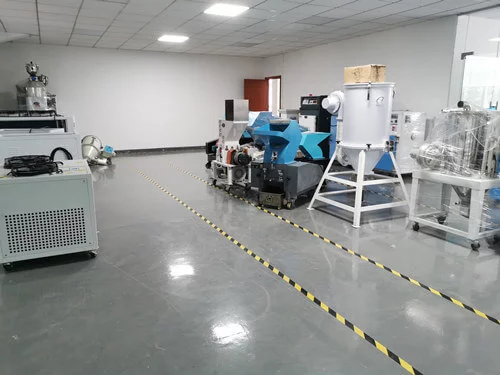
Knowledge Resource
Plastic auxiliary equipment plays a crucial role in the plastic manufacturing process by supporting primary machinery such as injection molding machines, extrusion systems, and blow molding machines. These auxiliary systems improve efficiency, ensure consistent production quality, and enhance overall operational workflow in plastic processing.
What is Plastic Auxiliary Equipment?
Plastic auxiliary equipment refers to the additional machinery and systems used alongside primary plastic processing machines. These tools perform vital functions like material handling, temperature control, and waste management, enabling manufacturers to optimize their operations and achieve high-quality output.
Types of Plastic Auxiliary Equipment
Material Handling Equipment
Material handling equipment ensures the efficient transport and preparation of plastic materials before processing.
- Hoppers and Loaders: Automatically feed raw materials into the processing machine.
- Conveyors: Transport materials or finished products across production lines.
- Silicone Dryers: Remove moisture from raw materials to prevent defects in finished products.
Temperature Control Equipment
Temperature control systems are essential for maintaining optimal processing conditions.
- Chillers: Cool the plastic components during and after processing.
- Mold Temperature Controllers: Maintain consistent mold temperatures to improve product quality and reduce cycle time.
- Cooling Towers: Provide efficient cooling for larger industrial setups.
Size Reduction Equipment
Size reduction equipment prepares waste or scrap materials for recycling.
- Granulators: Break down plastic waste into smaller, manageable pieces for reprocessing.
- Shredders: Handle large plastic pieces, turning them into smaller fragments.
- Pulverizers: Reduce plastics to fine powders for reuse.
Dosing and Mixing Equipment
Dosing and mixing machines ensure precise blending of raw materials, additives, and colorants.
- Volumetric Feeders: Measure and feed additives based on volume.
- Gravimetric Blenders: Accurately weigh and mix multiple material components.
- Batch Mixers: Blend large quantities of materials consistently.
Dehumidifying Equipment
Dehumidifiers remove excess moisture from plastic resins, improving the quality and consistency of molded products.
- Hot Air Dryers: Use heated air to dry materials before processing.
- Desiccant Dryers: Remove moisture from hygroscopic materials like ABS, PET, and PC.
Robotic Systems
Robotic systems automate tasks such as material handling, product sorting, and assembly.
- Pick-and-Place Robots: Improve accuracy and reduce manual labor.
- Robotic Arms: Perform complex tasks like trimming and finishing plastic products.
Applications of Plastic Auxiliary Equipment
Plastic auxiliary equipment supports various processes across multiple industries, including:
- Injection Molding: Ensures precise material dosing, cooling, and scrap management.
- Extrusion: Facilitates consistent material feeding and cooling for continuous production.
- Blow Molding: Supports material drying, temperature control, and product handling.
- Recycling: Aids in shredding, granulating, and reprocessing plastic waste.
Benefits of Using Plastic Auxiliary Equipment
Increased Efficiency
Auxiliary equipment automates repetitive tasks, reduces production downtime, and optimizes resource usage.
Enhanced Product Quality
By maintaining precise material handling, drying, and temperature control, auxiliary equipment ensures consistent product quality.
Cost Savings
Improved operational efficiency and material recycling reduce production costs and minimize waste.
Customization and Flexibility
Auxiliary systems can be tailored to specific production requirements, making them adaptable for different applications and materials.
Sustainability
Equipment like granulators and shredders supports recycling efforts, promoting eco-friendly manufacturing practices.
Factors to Consider When Choosing Plastic Auxiliary Equipment
- Compatibility: Ensure the equipment is compatible with your primary processing machines.
- Capacity: Choose equipment that matches your production volume requirements.
- Energy Efficiency: Opt for energy-efficient systems to reduce operational costs.
- Automation Level: Decide between manual, semi-automatic, or fully automated solutions based on your needs.
- Maintenance: Look for durable equipment with easy maintenance features to minimize downtime.
Conclusion
Plastic auxiliary equipment is essential for optimizing plastic processing operations. From material handling to temperature control and recycling, these systems enhance efficiency, improve product quality, and reduce costs. By selecting the right auxiliary equipment for your needs, you can streamline production, meet sustainability goals, and maintain a competitive edge in the plastic manufacturing industry.
